The titanium investment casting process is an essential manufacturing technique widely used across industries like aerospace, medical devices, and automotive for its precision, repeatability, and ability to create complex titanium components. As titanium becomes an increasingly popular choice of material due to its high strength-to-weight ratio, understanding this vital process enables smarter titanium casting investment decisions. We will analyze the key phases like wax pattern creation, ceramic shell building, melt pouring and post-finishing in the lost-wax titanium investment casting workflow along with its advantages over alternate titanium fabrication routes.
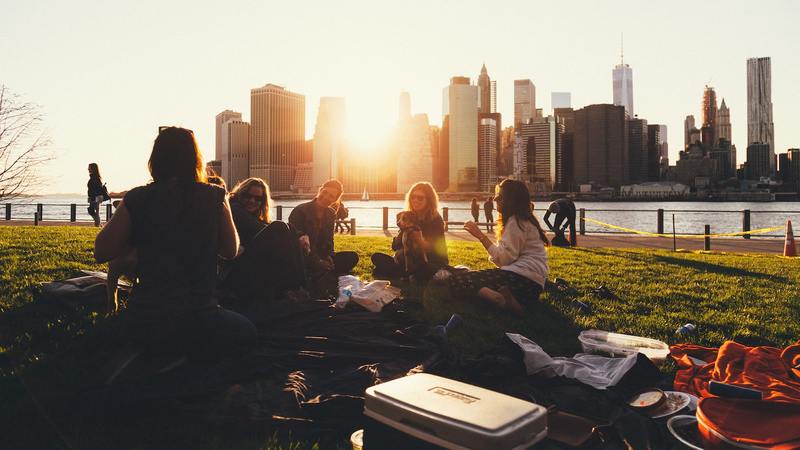
Creating reusable wax pattern tooling is critical first step in titanium casting process
The lost-wax titanium investment casting technique origins trace back over 6000 years ago to early bronze sculptures and jewelry castings. It starts with the fabrication of a wax pattern prototype of the final cast titanium component through injection molding. Constructing reusable wax injection dies rather than one-off wax models is essential for serial production. The wax material properties like flow, contraction provide vital clues in preventing defects. Other flexible pattern materials like plastic or frozen mercury can supplement traditional wax. But pattern design optimization considering specific finish tolerance, positional accuracy parameters for titanium alloys is an iterative process aided by simulations and rapid prototyping.
Building strong ceramic shell mold crucial to impede titanium-molten metal reactions
The vulnerable wax prototype requires support structures before undergoing molten titanium pouring at 1650 °C temperatures. So the wax component gets dipped multiple times in ceramic slurry mixtures of silica solids and binder solutions to fabricate a rigid outer shell. Modern zircon-based mixtures allow faster drying between layers. Shell thickness, smoothness level, and permeability are altered to counteract titanium alloy reactivity risks during casting. Using computational modeling informs the high-pressure steam dewaxing parameters as well. This ‘lost wax’ step gives this technique its name though residues necessitate thorough cleaning before proceeding.
Molten titanium pouring and solidification key to gain fine microstructures
The empty ceramic mold then undergoes firing above 800°C to develop handling strength and minimize thermal shocks during melt pouring. Controlled preheating also prevents titanium freezing too quickly. Induction guide or arc melting of mixed titanium alloys like Ti-6Al-4V under inert gas protection produces the molten metal pool for pouring through channels into the evacuated shell. Tighter compositional control distinguishes investment cast titanium alloys over other fabrication routes. Directional solidification via cooling controlling maximizes performance. Final knockout and cut-off steps remove the embedded titanium casting before finishing processes.
Secondary machining and inspection essential for quality investment cast titanium
Advancing numerical modeling capabilities permit predicting the final titanium component geometry, microstructure, defects earlier. Still post-cast hot isostatic pressing, heat treatments address uneven residual stresses and mismatches in mechanical properties. Investment cast titanium alloys exhibit outstanding strengths after such adjustments too. Follow-up subtractive milling, drilling, grinding, polishing meet tighter dimensional and surface finish specifications. Non-destructive testing methods confirm mechanical integrity too before final precision titanium component delivery meeting required certification.
Mastering the intricate four key links from wax prototyping to completing titanium component post-processing makes adopting the lost-wax investment titanium casting technique attractive for high-performance industrial applications. It permits manufacturing intricate or bulky titanium parts unviable through alternate routes despite steeper initial tooling costs. Advancing quality practices and automation will expand implementing titanium casting across more cost-sensitive segments also.