Investment casting, also known as lost-wax casting, is a metal casting process that can produce complex, high-precision parts like turbine blades used in jet engines. The use of investment casting in manufacturing turbine blades provides many advantages over traditional casting methods. This article will examine the investment casting process for turbine blades and discuss how it enables the production of blades with superior mechanical properties, dimensional accuracy, surface finish, and complex internal cooling features.
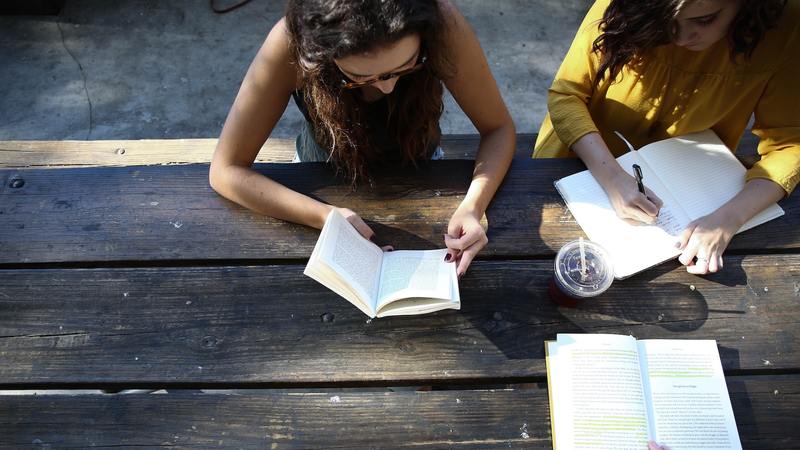
Investment casting process allows intricate blade shapes
The investment casting process starts with creating a wax pattern of the part to be cast. For a turbine blade, the wax pattern precisely replicates the airfoil shape and cooling channels inside the blade. This process works well for turbine blades because the wax can be injected into a die or 3D printed to achieve the complex geometry not possible with simple wax dipping. Once the wax pattern is created, it is surrounded by a ceramic slurry that hardens into the investment shell mold. The wax is then melted out, leaving behind a hollow mold matching the shape of the blade. Molten metal is poured into this mold to form the casting. The ceramic mold is broken away after solidification. This process allows for the production of thin-walled, hollow turbine blades with external aerodynamic shapes and intricate internal cooling passage geometries that would be impossible to achieve with conventional casting techniques.
Superior alloy properties with investment cast turbine blades
Investment casting enables the use of advanced nickel and cobalt based superalloys for turbine blades. These superalloys have excellent high temperature mechanical properties and corrosion resistance. The fine microstructures produced during solidification in investment molds yield superior alloy properties. Equiaxed and directionally solidified grain structures can be achieved. The rapid solidification rates attainable in investment molds also allow alloys with limited castability to be used. Advanced single crystal superalloys utilized in the latest turbine engines rely extensively on investment casting.
High dimensional accuracy reduces need for machining
The investment casting process results in turbine blades with excellent dimensional accuracy and surface finish. This reduces the need for extensive machining and coating operations after casting. Dimensional tolerances within 0.005 inches are possible for critical features like blade roots and shroud attachments. The surface finish from an investment cast turbine blade is much smoother than sand cast parts, minimizing airfoil roughness that causes performance losses. Leading and trailing edge profiles can be cast to final dimensions. Overall, investment casting turbine blades require far less machining than other casting processes, lowering costs.
Investment casting enables complex cooling features
Modern turbine blades require complex internal cooling channels and features like turbulators and pin fins to allow engine operation at extreme temperatures. These intricate cooling designs can only be produced using investment casting. The ceramic cores needed to form the cooling channels are readily incorporated into the investment mold. Cooling airflow modeling and analysis determines the optimal cooling configuration, which is then designed into the wax pattern and ceramic cores. This exemplifies a key benefit of investment casting – the ability to fabricate nearly unlimited internal features in cast parts.
Investment casting is vital for manufacturing the latest generation of turbine blades used in jet engines and industrial gas turbines. It provides the capability to produce blades with complex geometries, advanced alloys, high dimensional accuracy, and intricate cooling designs needed to withstand extreme engine temperatures. The investment casting process enables turbine blades that maximize engine performance and efficiency.