Investment casting, also known as lost-wax casting, is a manufacturing process used to create complex, high-precision metal parts. The process involves creating a wax pattern, coating it in ceramic slurry to create a mold, melting out the wax, and then pouring molten metal into the mold cavity. Proper tooling is critical for ensuring dimensional accuracy and achieving the right surface finish on cast parts. This includes wax injection dies, ceramic shell tooling, melt furnaces, and ancillary equipment. Using high-quality investment casting tooling enables tight tolerances, thin walls, and intricate geometries. It is an ideal process for complex parts made of alloys like stainless steel, cobalt, titanium, and superalloys. Investment casting tooling requires expertise to design and engineer. Factors like wax shrinkage, shell expansion, metal solidification, and secondary machining must be considered. With robust tooling in place, investment casting delivers durable and reliable metal components for demanding applications.
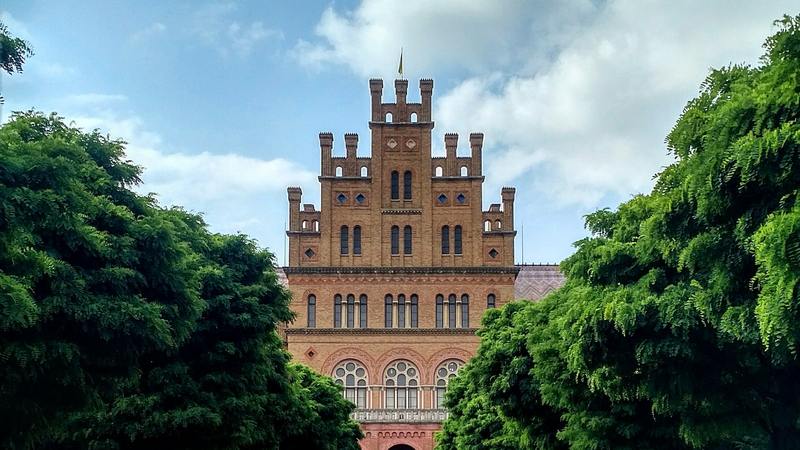
Wax tooling enables precision wax patterns for investment casting
The first step in investment casting involves fabricating a wax pattern, which is essentially a facsimile of the final metal part. Wax injection dies and associated tooling are used to mass produce the patterns accurately and consistently. The tooling includes dies, leader pins, ejector pins, and other components mounted in a base plate or chase block. Quality machining and polishing of these parts is essential for wax replication fidelity. The tooling must also incorporate fine details like draft angles and thickness transitions. Precisely injecting molten wax into the dies fills the cavity and creates the pattern. After cooling and solidification, the wax pattern is ejected and assembled if required. The tooling design and process parameters directly impact the dimensional conformity of patterns to specifications.
Ceramic shell tooling controls mold cavity dimensions
Once waxed patterns are ready, they are attached to a gating system and dipped in ceramic slurry to build a hardened shell mold. The tooling for this process includes dipping vessels, drain racks, stucco beds, and kiln fixtures. Strict control over variables like slurry viscosity, stucco size, and firing temperature is necessary to create molds with uniform wall thickness, integrity, and dimensional stability. The mold cavity must precisely replicate the wax pattern surface to yield castings with desired shape and tolerance. Pattern assembly jigs and trees are also important ceramic shell tooling elements. They position patterns optimally for even and efficient mold coverage during dipping rotations.
Melt and pouring tools deliver molten metal into the mold
After dewaxing to remove the wax pattern, the ceramic shell mold is preheated and filled with molten alloy using specialized equipment. Induction melting furnaces rapidly melt charge metal while minimizing contamination. They require refractory crucibles and power supplies to achieve proper superheat temperatures. Pouring tools including ladles, sleeves, and automated equipment then transfer and deliver the molten metal into the mold. These tools must resist high temperatures and facilitate smooth, full cavity filling to avoid turbulence and oxidation. They are made from materials like graphite, ceramics, and zirconia. For reactive alloys, vacuum pouring systems are used to prevent reactions like oxidation. Proper metal handling and delivery maximizes casting soundness and properties.
Secondary tooling generates final part configuration
Once the metal solidifies in the mold, the casting is removed and subjected to secondary operations like sprue removal, heat treatment, welding, finishing, and inspection. A range of cutting tools, jigs, fixtures, and gauges are required. This tooling must be engineered to high precision for finishing critical features, machining to net shape, and ensuring conformance to specifications. Grinding wheels, EDM electrodes, and custom cutting tools are involved. The final casting properties like strength, ductility, and microstructure are also controlled via heat treatment tooling. Overall, robust secondary tooling is vital for investment cast parts to meet functional requirements in end-use operating environments.
From wax injection dies to ceramic shell systems to melt furnaces and secondary machining, investment casting relies on specialized, high-quality tooling. This enables series production of dimensionally accurate, complex metal parts to serve critical applications across industries. With expertise in tooling design, process engineering, and quality control, investment casting delivers reliable, high-performance metal components.