Titanium investment casting has become an indispensable process for manufacturing high-performance titanium components across industries like aerospace, medical, and automotive. This advanced casting technique can produce complex, lightweight titanium parts with excellent mechanical properties and surface quality. In this article, we will explore why titanium investment casting is a smart investment for companies seeking to enhance product performance and reduce costs.
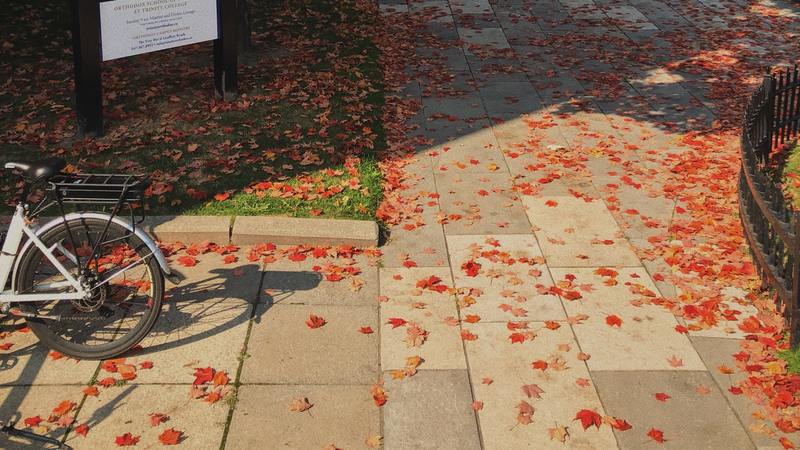
Superior Strength-to-Weight Ratio of Titanium Investment Castings
Titanium is revered for its outstanding strength-to-weight ratio, which exceeds that of steel and aluminum. Investment casting preserves the low density and high strength of titanium, enabling the production of lighter and stronger parts than traditional manufacturing methods. The aerospace industry relies on titanium investment castings for aircraft engine components to improve thrust-to-weight ratios. The medical sector uses cast titanium hip and knee implants that integrate well with the human body.
High Dimensional Accuracy and Surface Finish
The investment casting process involves creating a ceramic mold around a expendable wax pattern, allowing for products with excellent dimensional accuracy and smooth surface finish. This negates the need for extensive post-processing machining required with other manufacturing techniques. Companies can minimize material waste and total costs by utilizing near-net-shape titanium investment castings.
Design Flexibility for Complex Titanium Parts
Investment casting can produce highly complex titanium parts unattainable through other methods, with detailed features like thin walls, hidden voids, and curvatures. This design flexibility allows engineers to optimize components by concentrating material only where it is structurally required. Automakers employ titanium investment castings to reduce the weight of engine valves and turbocharger wheels.
Rapid Prototyping and Low Production Volumes
The investment casting process is ideal for rapid prototyping and low-volume production runs. It avoids the high upfront costs associated with machining or forging dies and molds required for manufacturing high volumes. Startups and R&D departments take advantage of investment casting titanium when designing and testing new product concepts that may change frequently.
Excellent Mechanical Properties
The regulated solidification and minimized impurities in investment castings result in titanium parts with outstanding ductility, fatigue strength, and fracture toughness compared to those produced through other methods. Components can be heat treated after casting to further enhance mechanical performance. The process allows alloy customization to meet specific application requirements.
Titanium investment casting enables lightweight, robust parts unmatched by other manufacturing techniques, explaining its rising adoption across sectors pursuing high-performance design. This versatile process will continue unlocking new titanium applications and driving innovation.