Investment casting, also known as lost-wax casting, is a specialized metal casting process used to create complex, high-precision metal parts. As demand rises for investment cast components across industries like aerospace, medical, and automotive, foundries and manufacturers need to stay updated on the latest equipment pricing trends to remain competitive. The price of investment casting equipment depends on several key factors including capacity, automation level, and origin country. With rapid technological advancements and fluctuating market dynamics, understanding the forces shaping equipment costs is essential for making sound investment decisions.
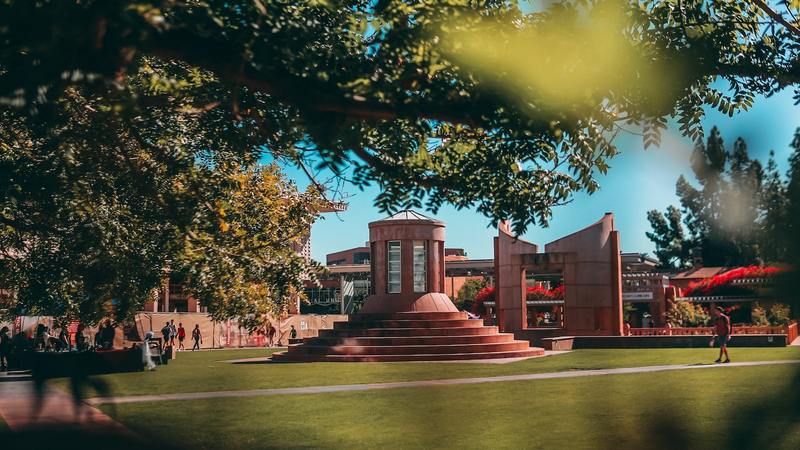
Capacity and size considerations significantly impact investment casting equipment pricing
The capacity and size of investment casting equipment is a major cost driver. Equipment with higher output capacity or able to handle larger components commands much higher prices. For example, an automated 10kg capacity vacuum induction melting furnace may cost $50,000 while a 100kg capacity unit runs over $500,000. Similarly, a small manual wax injector for jewelry casting may be just a few thousand dollars but large multi-ton machines for aerospace components can cost upwards of $1 million. When budgeting, foundries must align equipment size to their production volumes and part sizes to avoid overspending.
Level of automation is key factor influencing investment casting equipment costs
Automation carries a premium price but can improve consistency, efficiency, and safety. A fully automated casting line with integrated robotic arms, conveyors, and sensors costs multiples more than standalone semi-manual equipment. While automation increases upfront costs, it can deliver significant long-term savings in labor and improved quality control. The optimal level of automation depends on production volumes, variability, and the availability of skilled workers. With rapid advances in robotics and AI, automation costs are likely to become more affordable overtime as adoption increases.
Country of origin plays a role in investment casting equipment pricing
There can be major price differences between investment casting equipment manufactured domestically versus imported. In the U.S., local equipment manufacturers leverage proprietary technologies and charge a premium over Chinese or Indian competitors. For example, a U.S.-built electric vacuum furnace may cost 50-100% more than an equivalent imported model. However, domestic equipment often offers better after-sales support, shorter lead times, and may integrate better with existing production flows. Weighing origin costs against other factors like quality, support, and ease of integration is recommended when sourcing capital equipment.
Used and refurbished equipment provide budget-friendly investment casting solutions
The investment casting equipment market also offers used and refurbished machinery at substantial discounts to new equipment pricing. Reputable dealers inspect, upgrade, and guarantee quality at a fraction of the cost. While productivity and lifespan may be reduced, used equipment can be an attractive option for smaller foundries with limited budgets. When sourced through reliable channels, used machinery can deliver excellent value and performance.
Investment casting equipment is a major capital expenditure that must be carefully evaluated based on capacity needs, desired automation levels, country of origin, and multiple other factors that significantly influence pricing. With smart procurement decisions, foundries and manufacturers can acquire equipment aligned to their operational needs and budget realities. Used and refurbished equipment also offer affordable alternatives to boost capabilities without overextending limited capital resources.