Investment casting, also known as lost-wax casting, is a metal forming process that can produce complex, high-quality metal parts from alloy melts. It is considered one of the most cost-effective ways for manufacturing near-net-shape metal components with exceptional surface finish and dimensional precision. The use of investment casting with copper alloys has gained popularity in recent years due to its versatility in producing intricate copper components with superior mechanical properties. This article will provide an overview of the copper investment casting process and discuss its advantages in manufacturing complex copper alloy parts.
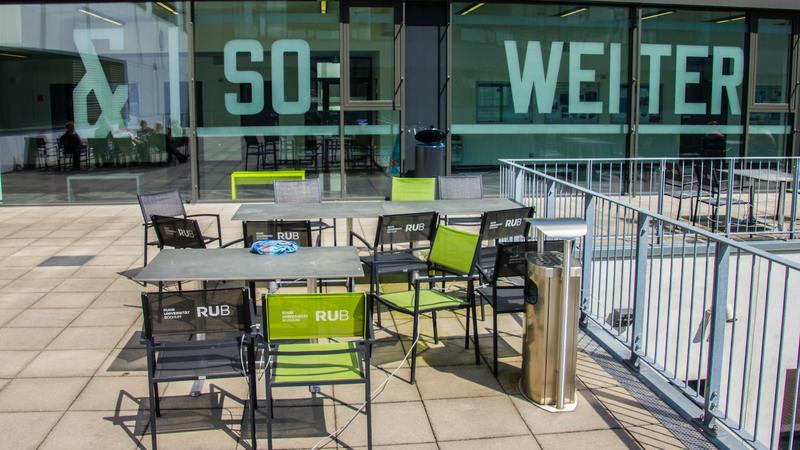
The steps involved in copper investment casting process
The copper investment casting process generally involves the following steps:
– Pattern making: A wax pattern is made by injecting melted wax into a metal die. The wax pattern is a replica of the final part to be cast.
– Mold making: The wax pattern is attached to a gating system and dipped multiple times in a ceramic slurry to build a hard ceramic shell around it. The ceramic mold then goes through a dewaxing process where the wax melts out.
– Pouring: The ceramic mold is preheated and molten copper alloy is poured into it to fill the cavity left by the melted wax. The metal takes the shape of the mold interior.
– Knockout and finishing: Once the metal solidifies, the ceramic shell is broken off to extract the casting. Then finishing operations like grinding and polishing are done to get the final cast product.
Advantages of copper investment casting
Some of the major advantages of using investment casting for copper alloy parts production include:
– Ability to produce complex geometries with undercuts, hollow sections etc. These would be difficult to achieve with other methods.
– Excellent surface finish and dimensional accuracy. The ceramic mold can pick up fine details from the wax pattern.
– Parts have low porosity and fewer defects. The ceramic shell controls the solidification process.
– Thin walls and exceptional mechanical properties can be attained. Heat treatment can further enhance properties.
– Wide range of alloys like brass, bronze etc. can be cast to get desired properties.
– No part-specific tooling required unlike die casting. This reduces lead time and costs for small batches.
Applications of copper investment castings
Some of the common applications where copper investment castings are used are:
– Impellers, valves, pump components in fluid handling
– Connectors, terminals, enclosures used in electrical systems
– Custom fasteners, gears, sprockets with complex shapes
– Decorative and art hardware like door handles, lamps, sculptures
– Heat exchangers and heat sinks requiring high thermal conductivity
The excellent fluid flow properties, corrosion resistance, thermal and electrical conductivity of copper alloys make them ideal for investment casting of critical components across industries like aerospace, defense, marine, oil and gas, chemical processing etc.
In summary, the copper investment casting process utilizes the lost-wax method to produce high-quality and complex copper alloy components with tight tolerances, superior finish and extensive customization. The ability to form elaborate contours makes it especially suitable for producing intricate shapes not possible with other casting methods. With its numerous advantages and material versatility, investment casting will continue to be an efficient production method for critical copper alloy parts.