Brass investment casting is an important metal casting process that has been widely used in various industries. It provides several advantages over other casting methods in terms of design flexibility, cost-effectiveness, and ability to cast complex components with tight tolerances. This article will introduce the basics of brass investment casting, analyze its key advantages, and explore the wide applications of brass investment casting in fields like aerospace, automotive, and medical equipment manufacturing. The unique benefits of brass investment casting make it an ideal choice for producing intricate metal parts with high accuracy. By gaining a comprehensive understanding of brass investment casting, manufacturers can make informed decisions when selecting the optimal casting techniques for their products.
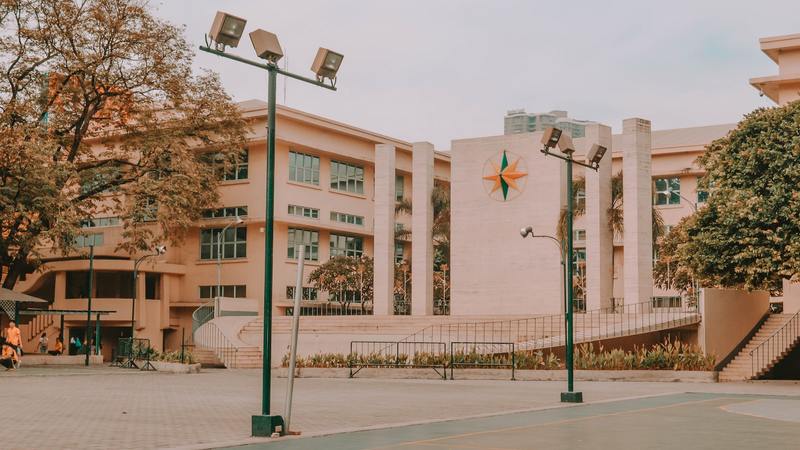
Brass investment casting enables complex geometries with high dimensional accuracy
One of the greatest advantages of brass investment casting is its unparalleled ability to produce complex shapes and geometries that would be impossible with most other casting methods. The use of a disposable wax pattern in investment casting allows for the creation of parts with incredibly complex features, internal passages, and thin walls. The ceramic mold formed around the wax pattern also enables excellent surface finish and dimensional tolerance control down to +/- 0.005 inches. These capabilities make brass investment casting suitable for manufacturing components with precision features and tightly controlled dimensions for fitting and assembly, which is critical for industries like aerospace and medical devices. The precision and design flexibility of investment cast brass parts allow engineers to optimize designs to reduce weight, improve performance, and lower costs without sacrificing quality.
Brass investment casting offers cost-efficiency for medium to high volume production
In addition to design flexibility, brass investment casting provides a cost-effective solution for producing medium to high volumes of complex metal components. The ability to cast multiple parts in a single ceramic mold reduces the unit cost as production volumes rise. While the initial tooling costs of investment casting can be higher than some other methods, the costs per part decrease significantly for large production runs. For example, investment casting is a better option than CNC machining for producing over 500-1000 units. The wax patterns can also be reused to amortize initial costs over longer production runs. Overall, brass investment casting delivers an economical production method for complex components when the volumes justify the initial mold tooling investment.
Superior material properties and finish for brass investment cast parts
Brass investment casting produces metal parts with material properties and finish quality unmatched by other casting processes. The controlled solidification results in fine-grained microstructure that enhances the strength, ductility and corrosion resistance of the cast brass components. The ability to cast highly detailed features reduces the need for secondary machining. And the surface finish directly from the mold is smoother and more lustrous than sand casting and other methods. These advantages lead to superior quality brass parts that require minimal additional processing. Investment casting also leaves no parting lines, flash or draft angles that need cleaning up. This combination of excellent material properties and surface finish make brass investment casting suitable for critical application components across industries.
Wide applications of brass investment casting across industries
The unique capabilities of investment casting have made it the process of choice for producing brass components and products across a diverse range of industries. In aerospace, brass investment castings are used for critical jet engine components, helicopter transmission housings, wing and fuselage fittings, landing gear parts, and interfaces for hydraulic and fuel systems. In the automotive industry, brass investment castings provide cost-effective production for turbocharger housings, exhaust components, fuel system parts, drivetrain yokes, suspension links, and steering knuckles. Other applications include impellers, valves and fittings for oil and gas, jewelry making, surgical instruments, marine hardware and a wide range of consumer product components.
Brass investment casting offers unrivaled design freedom, accuracy, material properties and cost-efficiency for manufacturing complex metal parts. Its unique advantages including tolerance control, surface finish, mechanical properties and flexibility to produce multifaceted geometries make brass investment casting an essential production method across aerospace, automotive, medical and many other high-tech industries.